-
-
-
Company Performance
-
Contact Us
Strengthening Safety Production | Equipment Division Advances 5S Management in Workshops
2024.11
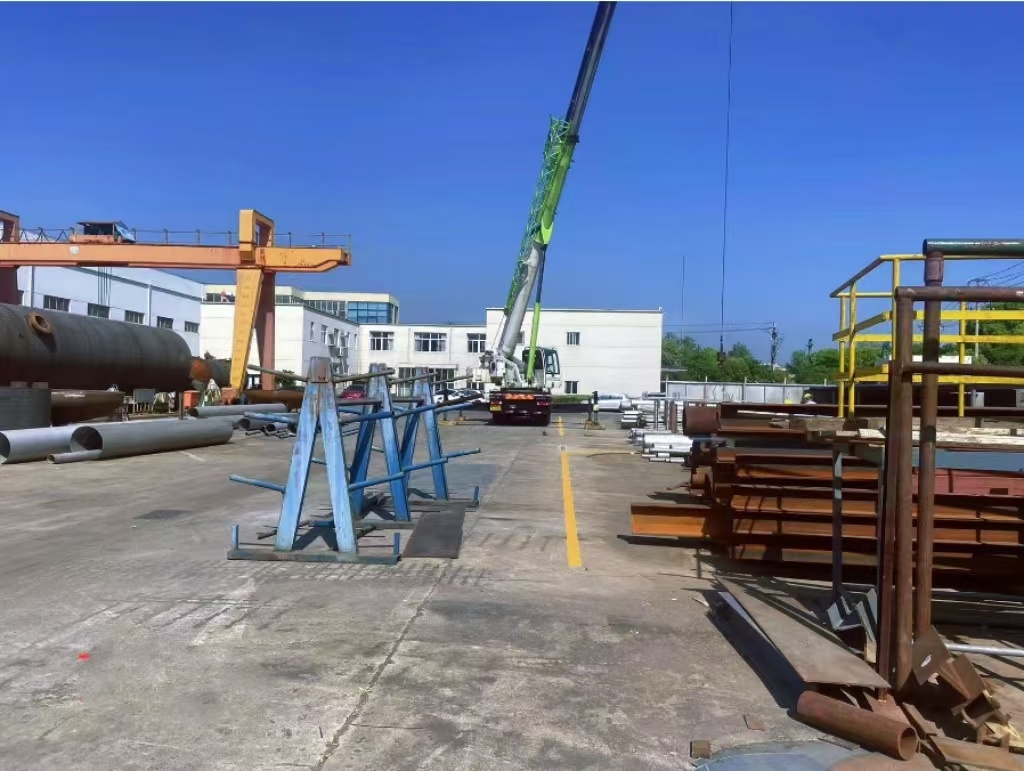
Across all workshops of the Equipment Division, a transformative initiative centered on 5S management is being rigorously implemented, building a robust foundation for workplace safety and operational efficiency. Let’s explore how the 5S methodology has taken root and delivered tangible results in the Equipment Division.
Lean 5S Management: From Concept to Action
Stepping into the Equipment Division’s workshops, you can immediately notice the clean, orderly environment—a stark contrast to the past, where tools and equipment were haphazardly stored, compromising both productivity and safety. Today, this scenario has been transformed through the systematic adoption of 5S, a Japanese-origin management philosophy.
1. Seiri (Sort)
The first step involves decluttering by separating essential items from non-essentials. Workshops underwent thorough cleanups, eliminating unnecessary materials and freeing up space. This not only improved workflow but also mitigated risks caused by chaotic storage.
2. Seiton (Set in Order)
Every tool and machine now has a designated location, with clear labels ensuring quick access for both new and experienced employees. Standardized layouts minimize safety hazards linked to disorganized workspaces or time wasted searching for tools.
Sweeping and Maintenance: Ensuring Safe and Efficient Operations
3. Seiso (Shine)
Regular equipment cleaning has become a routine practice. Maintaining spotless machinery not only prolongs its lifespan but also helps detect minor issues early, preventing small faults from escalating into major failures.
Cultivating Discipline: Building a Long-Term Safety Culture
4. Seiketsu (Standardize)
The first three steps are institutionalized into daily workflows, ensuring sustained orderliness. The Equipment Division has integrated 5S into standard operating procedures, with strict adherence to guidelines guaranteeing consistently safe and organized environments.
5. Shitsuke (Sustain)
Employees now embody disciplined work habits, prioritizing safety in every task. Awareness of safety protocols and efficiency has risen, fostering a collective responsibility for both personal performance and workshop-wide safety.
Remarkable Outcomes: Elevating Safety and Productivity
The persistent implementation of 5S has yielded significant results: workplace injuries have sharply declined, equipment downtime rates have dropped, and production efficiency continues to rise. These achievements underscore the effectiveness of 5S and reflect the Equipment Division’s unwavering commitment to safety.
Looking Ahead, the Equipment Division will deepen its 5S practices, refining workshop management to further support the company’s sustainable development. By fostering a culture of continuous improvement, Winner Group aims to set higher benchmarks in industrial safety and operational excellence.
Contact Us
E-mail :
hngc@jshuana.com
Phone No.:
Address:
Zhongxing Road, Xupu Industrial
Concentration Zone, Yizheng City
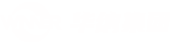
Phone No.: 0514-80850672
Email: hngc@jshuana.com
Address: Zhongxing Road, Xupu Industrial
Concentration Zone, Yizheng City
COOKIES
Our website uses cookies and similar technologies to personalize the advertising shown to you and to help you get the best experience on our website. For more information, see our Privacy & Cookie Policy
COOKIES
Our website uses cookies and similar technologies to personalize the advertising shown to you and to help you get the best experience on our website. For more information, see our Privacy & Cookie Policy
These cookies are necessary for basic functions such as payment. Standard cookies cannot be turned off and do not store any of your information.
These cookies collect information, such as how many people are using our site or which pages are popular, to help us improve the customer experience. Turning these cookies off will mean we can't collect information to improve your experience.
These cookies enable the website to provide enhanced functionality and personalization. They may be set by us or by third-party providers whose services we have added to our pages. If you do not allow these cookies, some or all of these services may not function properly.
These cookies help us understand what you are interested in so that we can show you relevant advertising on other websites. Turning these cookies off will mean we are unable to show you any personalized advertising.
Request Quote